gar
Senior Member
- Location
- Ann Arbor, Michigan
- Occupation
- EE
160215-2133 EST
Many tend to lump motor starting current into the term inrush current. The starting current to an induction motor is not comparable in form to the inrush current to a cold incandescent bulb or a transformer core driven into saturation.
In a motor there is a moderate air gap in the magnetic path and therefore it is difficult to produce conditions that saturate the core material.
Both incandescent bulbs and transformers have the possibility of initial inrush current that can be greater than 10 times the steady state current but only lasts about 1/2 cycle.
Starting an induction motor is like placing an inductor with internal resistance that does not easily saturate across the line. Basically a constant inductance with constant internal resistance.
For the definition of a split-phase induction motor see http://www.leeson.com/TechnicalInformation/sphase.html .
The waveforms that I show below are for an unloaded 1/3 HP split-phase motor.
For measurement I used a Rigol digital scope, a 10 A 50 mV shunt, and a Triac solid state switch. Input is a nominal 120 V, usually about 123 V. Scaling 100 V per major division for source voltage, 10 A per division for total motor current, and 10 millisecond per horizontal division.
If you look at the Leeson schematic you see two L/R paths in parallel. The starting coil path has a centrifugal switch that removes this path after the motor is near full speed. The starting coil path has a low L/R time constant which means it looks very resistive, and not very inductive. Thus, very little current phase shift. While the running winding has a much longer L/R time constant and its current has a much greater phase shift relative to the applied voltage. The two different phase shifts produce the two differnt magnetic vectors that create a rotating magnetic field for starting. This is a two phase motor for starting.
Without tearing the motor apart I can not separate the two currents for measurements. But the starting winding current is dominate and thus I can still show much of what is important relative to motor starting currnet.
You can not instantaneously change the current in an invariant inductor. Thus, I don't expect to see any large inrush current.
What is seen is a relatively constant current from the start with a gradual drop until the centrifugal switch opens. Then the current rapidly drops to a new level defined only by the run coil. For startup the phase shift for the combined pair of coils is about 20 deg, and for the run only coil about 70 deg.
Blue is motor voltage, and yellow is motor current.
.
See the motor voltage drop at start from the source impedance of the line to the motor. As current diminishes the voltage rises. At the 6th negative voltage peak the switch opens and a arc continues current flow until the voltage (current) zero crossing. After this we only have the run coil current with no appreciable mechanic load. Note: the large current phase shift.
If you add input impedance, then the time to reach speed is lengthened, but the starting current will be lower.
Remember all the above is without any additional mechanical load, We just have inertia, rolling, and windage friction.
.
Many tend to lump motor starting current into the term inrush current. The starting current to an induction motor is not comparable in form to the inrush current to a cold incandescent bulb or a transformer core driven into saturation.
In a motor there is a moderate air gap in the magnetic path and therefore it is difficult to produce conditions that saturate the core material.
Both incandescent bulbs and transformers have the possibility of initial inrush current that can be greater than 10 times the steady state current but only lasts about 1/2 cycle.
Starting an induction motor is like placing an inductor with internal resistance that does not easily saturate across the line. Basically a constant inductance with constant internal resistance.
For the definition of a split-phase induction motor see http://www.leeson.com/TechnicalInformation/sphase.html .
The waveforms that I show below are for an unloaded 1/3 HP split-phase motor.
For measurement I used a Rigol digital scope, a 10 A 50 mV shunt, and a Triac solid state switch. Input is a nominal 120 V, usually about 123 V. Scaling 100 V per major division for source voltage, 10 A per division for total motor current, and 10 millisecond per horizontal division.
If you look at the Leeson schematic you see two L/R paths in parallel. The starting coil path has a centrifugal switch that removes this path after the motor is near full speed. The starting coil path has a low L/R time constant which means it looks very resistive, and not very inductive. Thus, very little current phase shift. While the running winding has a much longer L/R time constant and its current has a much greater phase shift relative to the applied voltage. The two different phase shifts produce the two differnt magnetic vectors that create a rotating magnetic field for starting. This is a two phase motor for starting.
Without tearing the motor apart I can not separate the two currents for measurements. But the starting winding current is dominate and thus I can still show much of what is important relative to motor starting currnet.
You can not instantaneously change the current in an invariant inductor. Thus, I don't expect to see any large inrush current.
What is seen is a relatively constant current from the start with a gradual drop until the centrifugal switch opens. Then the current rapidly drops to a new level defined only by the run coil. For startup the phase shift for the combined pair of coils is about 20 deg, and for the run only coil about 70 deg.
Blue is motor voltage, and yellow is motor current.
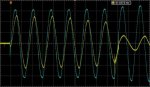
.
See the motor voltage drop at start from the source impedance of the line to the motor. As current diminishes the voltage rises. At the 6th negative voltage peak the switch opens and a arc continues current flow until the voltage (current) zero crossing. After this we only have the run coil current with no appreciable mechanic load. Note: the large current phase shift.
If you add input impedance, then the time to reach speed is lengthened, but the starting current will be lower.
Remember all the above is without any additional mechanical load, We just have inertia, rolling, and windage friction.
.