sdkokx
Member
- Location
- Grand Rapids, Michigan
Hello,
I have a motor running off of a VFD and we keep getting an Overload Fault on the inverter, what can I safely set the Thermal Overload to on the VFD for this motor? It's a 25hp motor on a 480v circuit. It is currently set at 38 Amps by default. I know standard FLA is 34 Amps but I also know that running at a lower frequency can result in higher current. This unit never goes above 51hz.
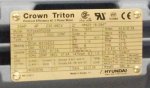
I have a motor running off of a VFD and we keep getting an Overload Fault on the inverter, what can I safely set the Thermal Overload to on the VFD for this motor? It's a 25hp motor on a 480v circuit. It is currently set at 38 Amps by default. I know standard FLA is 34 Amps but I also know that running at a lower frequency can result in higher current. This unit never goes above 51hz.
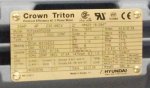